Inhoud
Het proces dat we orderpicken of orderverzamelen noemen, is het bijeenzoeken van artikelen en grondstoffen aan de hand van een bestelling. Het is een van de centrale taken in een magazijn. De bij het orderpicken gebruikte werkmethode is doorslaggevend voor tal van parameters, bijvoorbeeld de indeling van het magazijn, de toewijzing van opslagplekken, de organisatie van de intralogistiek en de keuze van geschikte transportbandtechnologie.
In dit artikel geven we u een overzicht van deze samenhang en de belangrijkste informatie over orderpicken: welke methodes zijn er, bij welk soort bedrijf passen ze en hoe kunnen ze in de praktijk worden toegepast of geoptimaliseerd.
Wat is orderpicken? Taken en definitie
In de logistiek wordt orderpicking gedefinieerd als een proces waarbij afzonderlijke goederen of artikelen uit het assortiment van een bedrijf worden samengevoegd tot een goederenpakket. Dat gebeurt op basis van bestellingen die rechtstreeks van klanten komen of intern van een andere afdeling van het bedrijf (bijvoorbeeld van de productie). Werknemers die deze orders in het magazijn verwerken worden orderpickers of -verzamelaars genoemd.
Samen met goederenontvangst, opslag, intern goederentransport en goederenuitgifte is orderpicking een deelgebied van de intralogistiek. Het omvat zelf ook verschillende processen, waaronder:
- Het lokaliseren van de bestelde artikelen in verschillende opslagzones
- De selectie van geschikte transportbanden, transportroutes en containers
- De goederen uit de magazijnstellingen nemen
- Het samenstellen van een goederenzending
- Het vervoer van de opslagplek naar de verpakkings- en verzendruimte
Er zijn verschillende manieren om het orderverzamelen in een bedrijf vorm te geven, afhankelijk van hoe complex de orderverwerking is. Een doorslaggevend criterium voor de gekozen methode is of een bedrijf grotendeels regelmatige, planbare bestellingen uitvoert of eerder incidentele, afzonderlijke orders. Ook andere parameters zoals de verscheidenheid aan goederen, de grootte van het magazijn, het volume van de zendingen en het type en de grootte van de te verzenden goederen spelen een rol. Voor elk scenario zijn er geschikte systemen, en kan er een methode worden gevonden om het verzamelen zo efficiënt mogelijk te organiseren.
Orderpicken: methodes voor het efficiënte verwerken van bestellingen
Om de optimale methode te vinden voor het orderpicken in uw bedrijf moet u kijken naar de binnenkomende orders. Uit de bestelhoeveelheden, het aantal verschillende artikelen en eventuele herhalingen van bestellingen is af te leiden welke methode leidt tot een soepele verwerking. U hebt de keuze tussen een- of tweestapsprocessen.
1. Eenstaps orderpicken
Bij eenstaps orderpicken wordt elke bestelling afzonderlijk uitgevoerd. Dit betekent dat alle afzonderlijke artikelen van een bestelling uit het magazijn worden gehaald en worden verpakt, voordat de volgende bestelling aan de beurt is. Bij deze procedure oriënteert men zich in principe op de binnenkomende orders, maar dit kan op twee verschillende manieren worden uitgevoerd.
- Ordergericht, in series orderpicken:
Alle bestelde artikelen worden afzonderlijk en in volgorde uit de opslagplaats gehaald. Afhankelijk van de grootte van het magazijn is hiervoor één persoon verantwoordelijk, die het hele magazijn doorloopt. Als alternatief kan de bestelling van een deel van het magazijn naar het volgende worden doorgegeven. Deze methode is gebruikelijk, maar heeft alleen zin in kleinere bedrijven met overzichtelijke opslagzones.
Hoe groter de bestellingen en magazijnen, hoe zwaarder de nadelen gaan wegen: terwijl de eerste variant gepaard gaat met lange afstanden en picktijden, kan de tweede leiden tot lange wachttijden en fouten tijdens de overdracht.
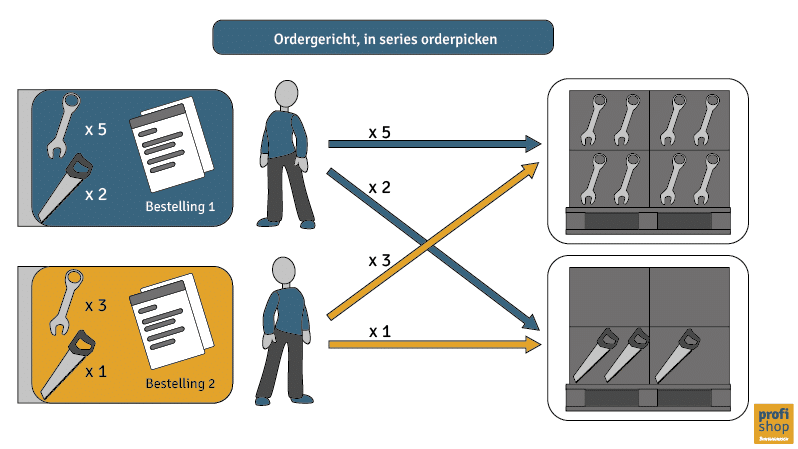
- Ordergericht, parallel orderpicken:
Hier werkt het personeel in verschillende delen van het magazijn tegelijk om een order te verwerken. De bestelling wordt uit alle afzonderlijke artikelen samengesteld op een verzamelpunt. Deze methode verkort de tijd die nodig is voor het orderpicken. Ze heeft echter het nadeel dat er een extra werkruimte nodig is om de artikelen bij elkaar te brengen. Ook kost het tijd om de samenwerking tussen de werknemers vooraf zo te coördineren, dat de taken goed zijn verdeeld en onnodige wachttijden in de afzonderlijke opslagzones worden voorkomen.
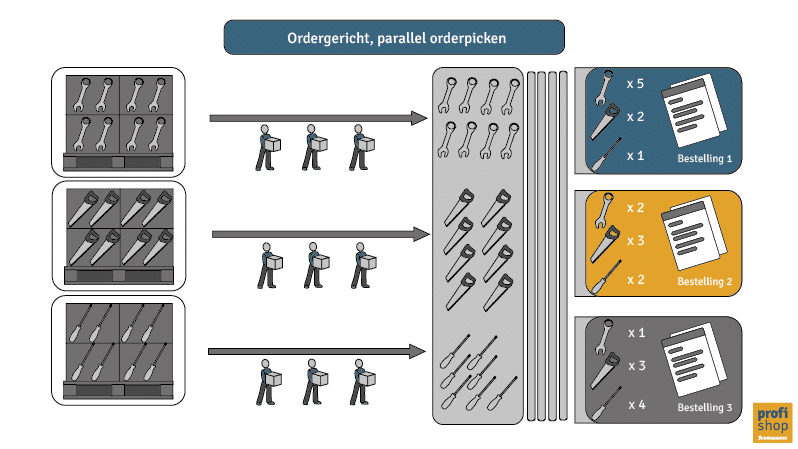
2. Tweestaps orderpicken
Als er meerdere orders voor dezelfde producten binnenkomen, is tweestaps orderpicken de betere keuze. Bij deze methode worden meerdere orders tegelijk verwerkt. De totale hoeveelheid te verzenden producten wordt uit het magazijn gehaald en pas in een tweede stap verdeeld over de afzonderlijke bestellingen.
Deze procedure wordt ook welparallel multipickengenoemd. Het effect hiervan is dat de afstanden en verplaatstijden die nodig zijn voor het orderpicken aanzienlijk korter worden, omdat de respectievelijke opslagplekken minder vaak hoeven te worden bezocht. Dit betekent niet dat een order per se sneller wordt afgehandeld: er moeten eerst meerdere bestellingen bij elkaar komen voordat het orderpicken plaatsvindt. De methode is daarom alleen efficiënt als sprake is van grotere bestelvolumes.
Een nadeel voor kleinere bedrijven is de grote organisatorische inspanning die ermee gepaard gaat. De bestellingen moeten eerst worden gegroepeerd aan de hand van de bestelde goederen, dan worden doorgestuurd naar de betreffende magazijnafdelingen en vervolgens weer worden opgesplitst in afzonderlijke leveringen. Voor grote postorderbedrijven is tweestaps orderpicken ideaal, omdat het heel goed kan worden toegepast in een geautomatiseerd magazijn waar centrale software alle bestellingen en verzendingen regelt.
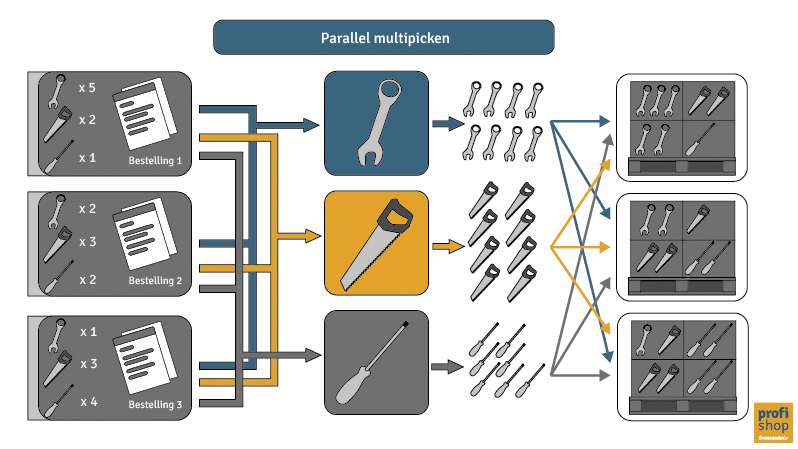
Orderpicksystemen: hoe vinden mens en product elkaar?
Een fundamentele vraag bij de magazijnindeling is: hoe willen we de goederen uit het magazijn verzamelen; handmatig of vertrouwen we op automatisch orderverzamelen?
Het antwoord op deze vraag heeft invloed op de inrichting en uitrusting van het magazijn, maar ook op de keuze van een geschikte magazijnstrategie, omdat die bepaalt hoe het personeel de voor verzending bestemde artikelen in handen krijgt. Er zijn twee manieren om dit te doen:
- Handmatig orderverzamelen: de verantwoordelijke magazijnmedewerker begeeft zich naar de opslagplaats van de goederen en pakt de bestelde hoeveelheid. Dit kan geheel zonder hulpmiddelen gebeuren, maar wordt meestal met behulp van handmatig bediende hefvoertuigen gedaan.
- In het geval van geautomatiseerd orderpicken worden de afzonderlijke goederen door robots of andere technologie uit de stelling gehaald. Voor het uitnemen en transport worden automatische systemen en transportbanden gebruikt, die de gewenste goederen rechtstreeks naar een verzamelplaats brengen. Afhankelijk van de mate van automatisering van het magazijn wordt het proces menselijk bediend of is het volledig softwaregestuurd.
De eerste variant maakt een grote mate van flexibiliteit mogelijk en is daarom bijzonder geschikt voor bedrijven met veel losse bestellingen. Met palletwagens en stapelaars kunnen ook grotere hoeveelheden goederen worden vervoerd.
Geautomatiseerde opties zijn daarentegen bij uitstek geschikt voor het besparen op tijd en personeel bij de afhandeling van planbare, grote bestellingen. Met een stellingsysteem bestaande uit magazijnstellingen maakt u optimaal gebruik van de opslagruimte. Met de juiste transporttechnologie kan zo’n stellingsysteem volledig automatisch worden beheerd.
U ziet hieronder een overzicht van de voor- en nadelen van beide systemen voor orderpicken.
Handmatig orderpicken | Automatisch orderpicken | |
---|---|---|
Voordelen | • Maakt het mogelijk flexibel te reageren op individuele wensen van de klanten • Snelle verwerking van bestellingen op korte termijn mogelijk • Onafhankelijkheid van software, technologie en elektriciteit • Lage investeringskosten • Kan gemakkelijk worden aangepast aan veranderende omstandigheden in het magazijn | • Snelle en efficiënte afhandeling van grote, terugkerende orders • Optimale transportroutes • Laag foutenpercentage, ook bij uitgebreid assortiment • Vaste orderpickstations vergemakkelijken het ergonomisch vormgeven van de werkplek • Het personeel wordt minder zwaar belast |
Nadelen | • Soms moeten lange afstanden worden afgelegd om een bestelling samen te stellen • Het orderpicken kost veel tijd • Foutenpercentage neemt toe met groeiend assortiment • Eventuele lange afstanden en zware goederen zijn belastend voor het personeel. | • Afhankelijkheid van elektriciteit en het functioneren van de machines • Hoge investerings- en onderhoudskosten • Niet de moeite waard als er sprake is van veel losse bestellingen met lage bestelvolumes • Vertraagde reactie op individuele orders op korte termijn |
Een orderpicktruck kan ondersteuning bieden bij het handmatig orderpicken. In deze video leggen we uit hoe een orderpicktruck werkt en hoe u hem bestuurt. We laten ook zien hoe u de accu moet opladen:
Orderpicken met of zonder bon
Als er in uw magazijn handmatig wordt gepickt, heeft u een methode nodig voor het documenteren van de goederenuitgifte. Zo kan het magazijnpersoneel zien welke goederen in welke hoeveelheid nodig zijn, en dit vormt de basis om de magazijnvoorraad naderhand bij te werken. De mogelijkheden variëren van een eenvoudige artikellijst om af te vinken tot hightech toepassingen:
- Pick-by-paper is de eenvoudigste vorm van orderpicken. Op een kopie van de order, een pakbon of een zogenaamde picklijst staan de hoeveelheid en soort goederen die nodig zijn. Het magazijnpersoneel vinkt de artikelen af. Later dienen deze papieren als ontvangstbewijs en wordt de informatie ingevoerd in de desbetreffende programma’s voor dataverwerking (magazijnvoorraad, facturering).
- Pick-by-scan is de meest gebruikte methode. De order wordt met alle relevante informatie (goederen, hoeveelheid, opslaglocatie) weergegeven op een mobiel apparaat. Het uitnemen van de goederen wordt geregistreerd met behulp van mobiele gegevensinvoer, bijvoorbeeld door het scannen van een barcode. De gegevens worden in realtime doorgestuurd naar de magazijnsoftware, zodat alle betrokken afdelingen altijd up-to-date zijn.
- Pick-by-voice werkt volgens een soortgelijk principe, maar dan volledig spraakgestuurd. De medewerker is uitgerust met een headset waardoor hij of zij hoort welke goederen moeten worden opgehaald; na het picken volgt een bevestiging. Ook de overdracht naar het softwaresysteem gebeurt automatisch en in realtime.
- Pick-by-light is een methode waarvoor u een speciale magazijninrichting nodig heeft. De stellingen of kasten zijn uitgerust met een klein lampje, een hoeveelheidsindicator en een bevestigingsknop. Het lampje geeft aan dat goederen van deze locatie moeten worden verwijderd. Als het artikel van de plank is genomen, wordt de knop ingedrukt en meldt het systeem dat de bestelling is uitgevoerd en de inventaris is bijgewerkt.
- Pick-by-vision is een van de nieuwste methodes van orderpicken. Hierbij wordt alle relevante informatie weergegeven en geregistreerd met behulp van digitale brillen. Op basis van het gezichtsveld van de persoon herkent de bril welke informatie nodig is en geeft deze weer (bijv. exacte opslaglocatie, hoeveelheden enz.). Wanneer de goederen worden uitgenomen, controleert een automatische visuele inspectie de hoeveelheid en het type goederen, vergelijkt ze met de bestelling en bevestigt meteen of alles compleet is.
Bij de pick-by-paper-methode wordt elke stap schriftelijk gedocumenteerd en vervolgens met behulp van deze documenten in de bijbehorende programma’s geregistreerd. Dit heeft het voordeel dat er geen uitgebreide planning of technische hulpmiddelen nodig zijn voor het orderpicken en dat nieuw personeel snel kan worden ingewerkt.
Uit de populariteit van methodes die gebaseerd zijn op mobiele gegevensinvoer blijkt: papierloos picken geniet vaak de voorkeur. Vooral in grote magazijnen met een hoge omloopsnelheid heeft dit veel voordelen: papierloos orderpicken vermindert de administratieve rompslomp en ook het foutenpercentage, omdat belangrijke informatie rechtstreeks wordt doorgestuurd. Dit heeft een positief effect op de tijden die nodig zijn voor het orderpicken, en op termijn ook op de opslagkosten. Anderzijds brengt de invoering van papierloze methodes hoge investeringskosten met zich mee, die voor veel midden- en kleinbedrijven niet in verhouding staan tot hun inkomsten. Daarom zullen beide methodes in de toekomst waarschijnlijk naast elkaar blijven bestaan.
Tijden voor orderpicken berekenen en optimaliseren
Bij de beoordeling van de efficiëntie van het orderverzamelen in een bedrijf gaat het altijd om de picktijden. Deze geven aan hoe snel de binnenkomende order in het magazijn wordt verwerkt. Wanneer de magazijnprocessen op de proef worden gesteld, worden vooral de picktijden onder de loep genomen, omdat hier een groot potentieel voor optimalisatie ligt. Het doel is altijd om zoveel mogelijk tijd te besparen en zo de kosten te verlagen.
Om de analyse te vergemakkelijken, wordt de totale picktijd onderverdeeld in vijf afzonderlijke tijden.
- Basistijd: tijd besteed aan de organisatie van het orderpicken (toewijzing van taken, verzamelen van documenten, beschikbaar stellen van transportbanden en containers, documentatie, enz.)
- Verplaatsingstijd: tijd besteed aan het afleggen van de weg van het startpunt naar de opslaglocaties en terug naar het verzamelpunt.
- Uitnametijd: tijd die nodig is om de opgeslagen goederen uit te nemen, transportcontainers te vullen of op het transportsysteem te plaatsen/vast te zetten
- Dode tijd (secundaire tijd): tijd voor alle secundaire taken die rechtstreeks verband houden met picken (zoeken naar de opslaglocatie, tellen van de hoeveelheid, controleren op volledigheid)
- Overige tijd: tijd die wordt besteed aan improductieve activiteiten tijdens het verzamelen (wachttijd, koffiepauze, praatje, toilet)
Als u deze tijden precies bijhoudt en bij elkaar optelt krijgt u de picktijd.
Picktijd = basistijd + verplaatsingstijd + uitnametijd + dode tijd + overige tijd
Deze formule is een vereenvoudiging van het proces van orderpicken; in de praktijk moet worden opgemerkt dat sommige van deze deeltijden overlappen. Verplaatsings-, uitname- en dode tijd moeten bij het verzamelen van een order voor elk artikel afzonderlijk worden geregistreerd en opgeteld. Hoeveel individuele activiteiten hier nog bij komen onder ‘overige tijd’, hangt af van de persoon die pickt. Alleen de basistijd wordt slechts eenmaal geteld bij het verzamelen van een order.
Na de berekening vindt de analyse plaats. De vraag is of en hoe de tijden verkort kunnen worden om opslagkosten te besparen. De onderverdeling in afzonderlijke tijden en activiteiten is hierbij nuttig, omdat u op die manier gemakkelijk kunt begrijpen welke processen al efficiënt verlopen en waar er nog ruimte voor verbetering is. In principe is er voor alle afzonderlijke categorieën zijn mogelijkheden om tijd te besparen, zoals uit de volgende voorbeelden blijkt:
Tijden | Mogelijkheden voor optimalisatie |
---|---|
Basistijd | • Een nieuw ontwerp voor de bonnen dat uniform en makkelijker te begrijpen is • Overstappen op papierloos orderpicken • Terbeschikkingstelling van voldoende transportmiddelen en -kisten • Gebruik van efficiënte software voor magazijnbeheer |
Verplaatsingstijd | • Aanpassen van de magazijnstrategie • Populaire of vaak gezamenlijk bestelde artikelen dicht bij elkaar opslaan • Route-geoptimaliseerde bestellijsten |
Uitnametijd | • Opslagruimte afstemmen op artikelen • Gemakkelijke toegang tot goederen waar veel vraag naar is • Plaats zware, onhandelbare artikelen binnen handbereik van transportbanden |
Dode tijd | • Magazijngangen en stellingvakken duidelijk markeren en zichtbaar maken • Gebruik indien nodig digitale orderpickingmethodes (pick-by-vision) |
Overige tijd | • Optimale coördinatie van processen in het magazijn om wachttijden te voorkomen. • Goede arbeidsvoorwaarden (eventueel een beloningssysteem) om het personeel te motiveren |
Meestal hebben verplaatsings- en uitnametijden het grootste optimalisatiepotentieel. Dit betekent dat maatregelen op deze gebieden ook het grootste effect hebben op de efficiëntie van het magazijn.
Veelgestelde vragen over orderpicken
Orderverzamelen is een onderdeel van de intralogistiek in bedrijven. Het omvat alle processen voor het verzamelen van individuele items van een bestelling uit het gehele goederenassortiment. Dit omvat:
• de lokalisatie van de bestelde artikelen in verschillende delen van het magazijn
• de selectie van geschikte transportbanden, transportroutes, containers enz.
• de verwijdering van de goederen uit het opslagrek
• de samenstelling van de goederenzending
Nadat alle artikelen uit het magazijn zijn gehaald en verzameld, worden ze aan de klant geleverd of naar de productieafdeling gestuurd.
1. De bestelling komt binnen
2. Samenstellen van de pakbon (eventueel rekening houdend met de routes).
3. Doorsturen naar de verantwoordelijke picker(s) (indien nodig naar meerdere opslagzones tegelijk)
4. Orderpicker gaat met met transportmiddel of -container naar de opslagplaats en neemt de goederen uit
5. Samenstelling van de volledige bestelling op een verzamelpunt
6. Overdracht voor transport
• Pick-by-paper: met pakbon of picklijst
• Pick-by-scan: met mobiele terminal en barcodescanner
• Pick-by-voice: uitsluitend spraakgestuurd via een headset
• Pick-by-light: verlichting en displays op de schappen in het magazijn geven aan welke artikelen moeten worden verzameld en in welke hoeveelheden
• Pick-by-vision: met digitale brillen die relevante informatie weergeven en de uitslag van goederen controleren (type, hoeveelheid).
Bij zogenaamd document-based picking worden alle stappen schriftelijk gedocumenteerd met de bijbehorende papieren (gedrukt en handgeschreven). Vervolgens vindt de overdracht naar bestanden of dataverwerkingsprogramma’s van de betrokken afdelingen plaats.
Bij papierloos orderpicken worden deze stappen digitaal en soms zelfs in realtime uitgevoerd. Enerzijds bespaart dit werktijd voor documentatie en administratie, anderzijds kan het foutenpercentage bij het picken aanzienlijk worden verminderd.
Bron afbeelding:
© Jungheinrich AG